What is DMAIC
📌 DMAIC is a methodology for optimizing business processes, derived from the Lean management and production principles.
The DMAIC process is composed of five stages: Define, Measure, Analyze, Improve, and Control. These steps help identify the root causes of inefficiencies and devise ways to enhance operations based on the data collected.
❗ It is commonly used to assess manufacturing and other physical, non-digital businesses.
Developed by statistician Walter A. Shewhart in the 1930s, this methodology is also closely linked to the well-known PDCA cycle, also referred to as the Deming Cycle, Shewhart Cycle, or Deming-Shewhart Cycle.
Key Stages of the DMAIC Process
Again, DMAIC stands for Define, Measure, Analyze, Improve, and Control. These five phases guide a business process through structured analysis to uncover areas for optimization.
Let’s dive deeper into each stage.
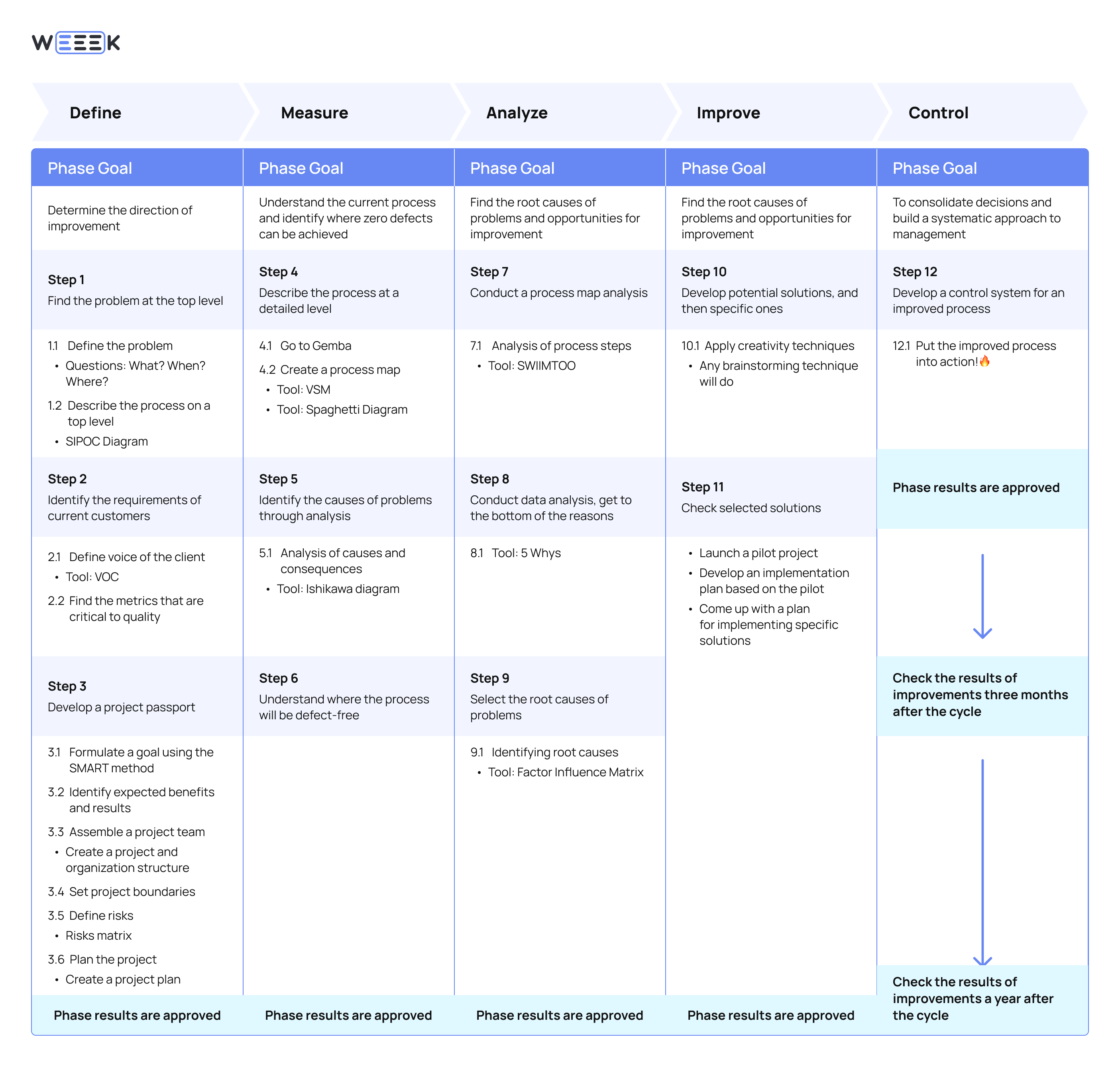
Define — Identifying the Problem
The first step is to clearly define the problem and understand why optimization is needed. Equally important is gaining insight into the customer and key stakeholders.
This phase can be broken down into three steps.
Step 1: Define the Problem and Process at a High Level
Start by addressing three key questions: What is the problem? Where does it occur? When does it happen? Then, use a SIPOC diagram to visualize the process at a high level.
Step 2: Identify Customer Requirements
Develop a plan to capture the Voice of the Customer (VOC). VOC is a tool used to understand customer needs and expectations, ensuring you retain loyal customers. This feedback is typically gathered through surveys, interviews, and reviews.
Step 3: Create a Project Charter
Also known as a project summary or business plan, the charter outlines the project’s objectives, scope, and key deliverables, serving as a roadmap for the optimization process.
Measure — Gathering Data
In this phase, the goal is to collect accurate and reliable data about the process. These insights help monitor progress, measure success, and ensure the project stays on track.
Here are the key steps.
Step 1: Map the Process in Detail
Start with a Gemba walk, a practice from Lean methodology, which involves visiting the actual location where work is done. For instance, if DMAIC is being applied to a delivery service, the manager should visit the warehouse where items are packed.
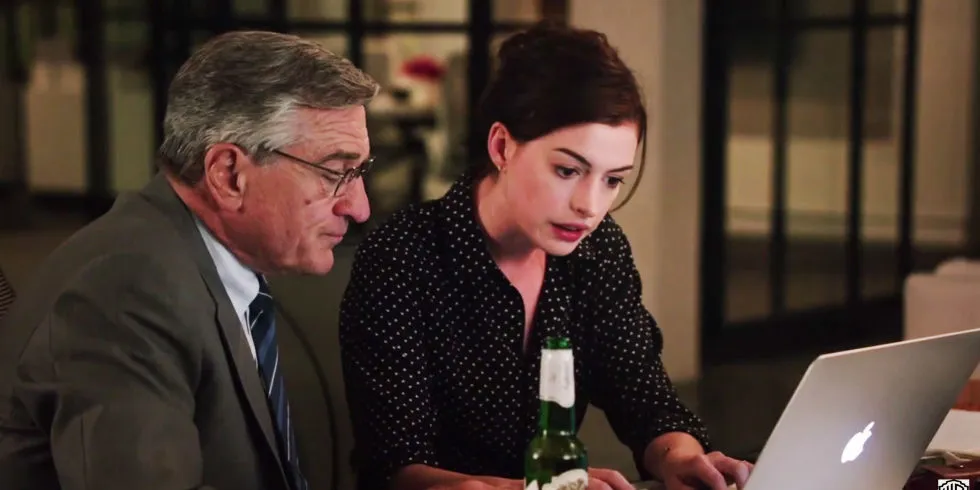
Next, develop process maps like the Value Stream Map (VSM) and a Spaghetti Diagram.
Step 2: Identify Potential Causes of Risk
Use the Ishikawa, or "fishbone" diagram, to analyze the potential causes of risks. This tool highlights how primary and secondary causes link to potential issues within the process.
Step 3: Assess Process Defect-Free Performance
Analyze data to understand when the process will be capable of consistently meeting customer expectations without any defects or issues.
Analyze — Identifying the Root Cause
This phase focuses on pinpointing the source of the problem based on the work done in the earlier stages. The goal is to understand what’s going wrong and why. The key steps include:
Step 1: Analyze the Process Map
Review the detailed process maps to locate inefficiencies and problem areas.
Step 2: Analyze the Data
Examine the data collected in previous phases to uncover patterns, inconsistencies, or areas where performance falls short.
Step 3: Identify Root Causes and Create a Factor Influence Matrix
Use tools like the “Five Whys” and the Ishikawa (fishbone) diagram to dig deeper into the root causes. Additionally, apply SWIIMTOO analysis to assess business losses and process inefficiencies.
Improve — Implementing Solutions
After identifying the root causes, the focus shifts to finding and testing solutions to improve the process.
Step 1: Generate Potential Solutions
Use creative techniques such as brainstorming and Six Thinking Hats to develop a wide range of possible solutions. The team should then filter and prioritize these ideas based on their feasibility and potential impact.
Step 2: Test and Implement Solutions
- Pilot Testing
Implement a small-scale pilot project to test the most promising solutions. It’s essential to continue monitoring performance and regularly meet to discuss results.
- Implementation Plan
Based on the pilot outcomes, refine the approach and create a detailed plan for full-scale implementation.
- Full Implementation
Roll out the chosen solutions, with the team closely monitoring progress and evaluating the effects on process performance.
Control — Ensuring Long-Term Success
The Control phase is an ongoing, sometimes never-ending, effort to ensure the improved process remains stable and efficient over time.
One Key Step: Develop a Control System
As the improved process moves into daily operations, the goal is to ensure that the progress and enhancements are sustained. After so much hard work, it’s crucial that the improvements aren’t lost.
A key tool here is the 5S methodology, which focuses on five essential principles: Sort, Set in order, Shine, Standardize, and Sustain. This system helps maintain order and efficiency in the workplace. For more details, you can explore this method in a dedicated article.
In addition, feedback mechanisms such as customer reviews, complaints, and suggestions play a vital role. It’s also important to gather input from the team using the new process, as they can provide valuable insights into its effectiveness or suggest further refinements.
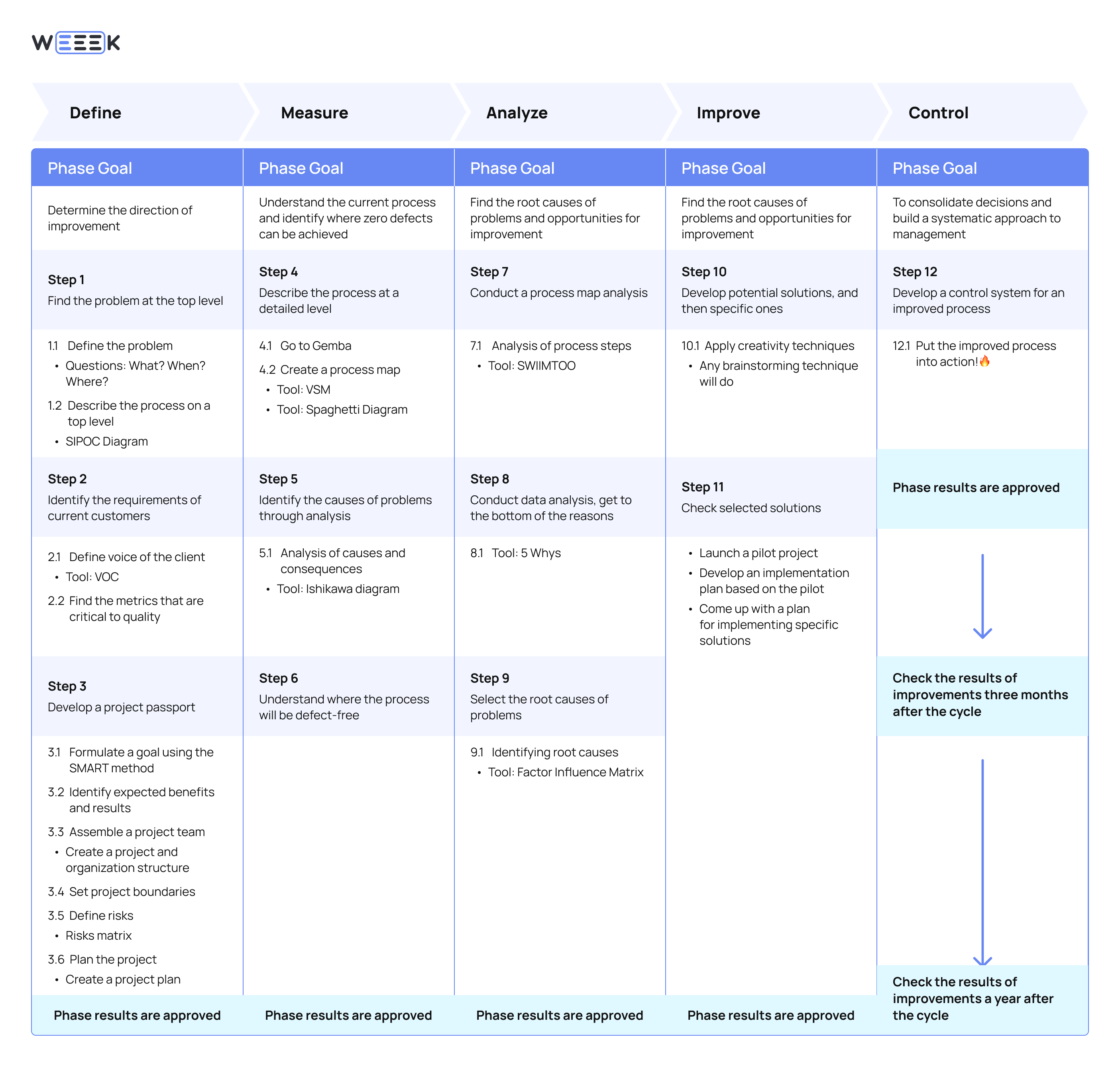
The Concept of Six Sigma and DMAIC
Six Sigma is a production management concept aimed at optimizing and improving processes while reducing defects. It is based on the philosophy of lean manufacturing.
The term "sigma" comes from probability theory, where it represents the symbol for error or deviation from a standard value.
☝🏻 The key focus of Six Sigma is customer satisfaction with the final product. Any defects or deviations from established norms—referred to as "sigmas"—should be kept to a minimum. Although there can be various quality levels, the number six is symbolic, representing the average deviation level in processes.
In Six Sigma, there are two main approaches to implementing the concept:
- DFSS (Design for Six Sigma) for projects and products that are still in development
- DMAIC for improving existing projects
Within the Six Sigma system, DMAIC helps build a roadmap for project development over several steps, adhering to the philosophy that preventing deviations is easier than correcting them.
Strengths of DMAIC
✅ Highly Structured Problem-Solving Approach
DMAIC offers a clear, step-by-step framework for addressing and resolving issues. This structured methodology ensures that, by following each phase methodically, organizations can effectively solve problems and achieve sustainable improvements.
✅ Data-Driven Decision Making
One of DMAIC’s core strengths is its reliance on data. Decisions are made based on thorough data collection, analysis, and interpretation, reducing reliance on guesswork or intuition. This ensures that solutions are grounded in factual, reliable information.
✅ Strategic Alignment
DMAIC projects are often chosen because they align with the organization’s broader strategic goals. This means that solutions are not only focused on fixing immediate problems but also contribute to the company's overall direction and long-term success.
✅ Improves Customer Satisfaction and Loyalty
Because DMAIC aims to minimize defects and enhance process quality, the end result is often higher-quality products and services. By aligning business processes with customer expectations, DMAIC can significantly boost customer satisfaction and loyalty, giving businesses a competitive edge.
Common Mistakes in Using the DMAIC Methodology
❌ Lack of Executive Support
One of the most critical errors is failing to secure strong backing from top leadership. Without robust support from senior management, teams can face resource shortages, resistance from various departments, and struggle to implement necessary changes. Active engagement from leadership is crucial for overcoming these obstacles and ensuring success.
❌ Vague Problem Definitions
Poorly defined or ambiguous problems result in ineffective solutions. If the problem isn’t clearly articulated, the team may waste time and resources on the wrong issues. To avoid this, it's important to invest time in crafting precise, measurable problem statements. Techniques like the “Five Whys” are especially useful for this purpose.
❌ Skipping the Measurement Phase
Sometimes teams rush through or even bypass the Measure phase, assuming they already understand the process. This can lead to missing the actual problem or making incorrect conclusions. Proper measurement is essential to gain accurate insights and drive meaningful improvements.
❌ Overemphasis on Tools
Focusing too much on the DMAIC tools while neglecting the culture of continuous improvement is another common mistake. It’s vital to cultivate an environment where employees are encouraged to seek out new opportunities for growth and improvement, rather than relying solely on process tools.
When to Use DMAIC
DMAIC is most effective when certain project and process characteristics are present:
- Existing projects and processes. DMAIC is ideal for improving processes that are already in operation.
- Recurring problems. If the same errors or issues keep cropping up, it's a clear indication that process improvement is needed.
- Unclear root causes. When the reasons behind recurring problems are not obvious or difficult to identify at different levels of the organization.
- Need for comprehensive audits. When there’s a need for a thorough audit of processes and business operations.
To determine whether DMAIC is the right tool, many companies add an unofficial preliminary step called Recognition. This step helps evaluate whether DMAIC is appropriate for the project by asking these questions:
- Is there a clear problem with the current process? If the problem can’t be clearly identified, using DMAIC to find a solution may be challenging.
- Is there potential to reduce process time or defects while improving key factors like cost savings and productivity?
- Are the processes being analyzed measurable? Do they involve quantifiable data, and can the results be expressed numerically?
If the answers to these questions are yes, DMAIC is likely a good fit for improving the process. If not, other methods such as Kaizen, 5S, Kanban, or the PDCA cycle might be more appropriate.
❗ DMAIC is not suited for developing new products or addressing minor issues. It’s also not effective when the root cause of a problem is beyond the company's control or difficult to uncover.
Key Points Summary
- DMAIC is a core component of the Six Sigma lean methodology and is used to improve existing processes
- The DMAIC cycle consists of five phases, each broken down into multiple steps
- Completing the DMAIC cycle provides a company with a comprehensive analysis of its current state and a roadmap for improvements. Skipping any steps can jeopardize the effectiveness of the process
- Successful DMAIC implementation requires strong leadership support; without it, there will be a lack of resources and momentum for improvements
- DMAIC is not suitable for launching new products or addressing minor issues